加工したワークの寸法測定を自動化するには【金型製造の場合】

Cimatron課の戸村です。
加工したワークの寸法測定でお困りではありませんか?
特に金型製造において、寸法測定を自動化することは簡単ではないと聞きます。
金型部品には勾配のついた面や曲面をもつ部品があるためです。
また各部品の加工数は1~数個と少なく、部品の種類が多いことも自動化が難しい要因と考えられます。
実は加工機を測定機代わりにすることによって、寸法測定を自動化&無人化できる方法があります。
ここでは、加工機を使った寸法測定を自動化するポイントや必要なものなどについて説明します。
これからご説明する内容は、以下に該当される方を対象としています。
- 様々な形状の部品を少ない数だけ加工されている(金型製造など)
- 自動工具交換(ATC)装置と数値制御(NC)が付いたミーリング加工機を使用している
いわゆるマシニングセンターです。NCフライス盤、NC旋盤は対象外です。
- タッチプローブで加工素材の原点出しをされている
加工されたワークを加工機上に置いたまま寸法測定することを「機上測定」と言います。
加工機を測定機代わりに利用することで、自動測定が可能となります。
機上測定&自動測定によって、無人運転が可能となります。
切削加工~寸法測定までを自動化&無人化することで、作業者の負担を軽減でき、工数とコストが削減できます。
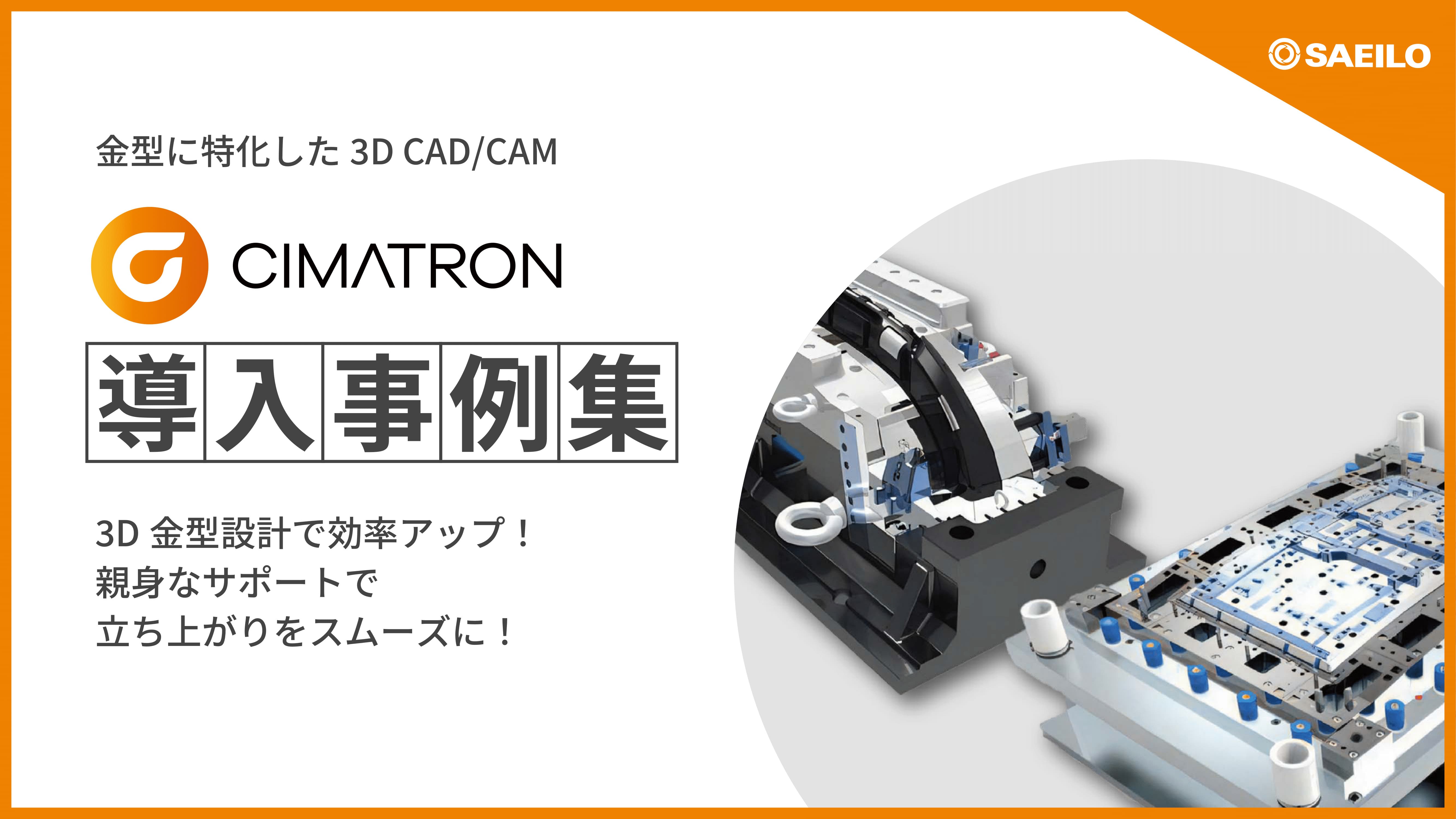
目次
加工ワークの寸法測定を自動化するポイント
1.加工機を測定機にする(機上測定)
マシニングセンターと呼ばれるミーリング加工機は、測定機代わりにすることが可能です。
ただし、加工機の仕様上できない場合があります。
測定機代わりにできる理由は3つあります。
理由1)3次元測定機と同様のタッチセンサーが使える(タッチプローブ)
加工機用のタッチプローブが使用できます。
このタッチプローブは、3次元測定機で使われているタッチプローブと同様のタッチセンサーです。
理由2)3次元測定機と加工機の構造が類似している
3次元測定機と加工機のハードウェアを比較すると、その構成要素はかなり似ています。
どちらも同様の構成要素を持っています。
- 駆動軸(X軸、Y軸、Z軸)
- タッチセンサー(タッチプローブ)
理由3)ソフトウェアの違いを補える
3次元測定機と加工機の大きな違いは測定機能です。つまりソフトウェアの違いです。
加工機は測定機能が不足しています。これは「測定プログラム」で補うことができます。
加工機の測定プログラムは、加工機が認識できるプログラムコードで記述します。
2.測定対象の加工ワークを動かさない
自動化には人が関わる「作業」を取り除くことが必要です。その一つが測定のための「ワーク移動」です。
このワーク移動を取り除く方法は2つ考えられます。
- 自動化できる設備を導入する(ロボットアーム+自動搬送装置など)
- 加工機上で寸法測定する
加工機上で寸法測定ができれば、ワークの移動が不要となります。(上記2)
更に追加工時のワーク移動も不要となります。
また、次の作業も不要となります。
- 3次元測定機上での原点出し作業
- 追加工での原点出し作業
いずれも人が関わる「作業」です。
3.3次元のモデルデータを利用する
勾配面や曲面のある加工ワークを測定するために、3次元モデルが必要です。
一般的にはソリッドモデルが適しています。サーフェイスモデルでも可能です。
3次元モデルが必要な理由は3つあります。
理由1)接触するタッチプローブの位置を取得するため
タッチプローブの先端は球になっています。
そのため、測定したい点にタッチプローブの先端球を正確に接触させる必要があります。
この時のタッチプローブの位置を得るために、3次元モデルが必要です。
理由2)タッチプローブの安全な位置や軌道を確認するため
タッチプローブが安全な軌道を通るかどうかを確認するために、加工ワークの3次元モデルが必要です。
タッチプローブの軌道と、加工ワークとの位置関係を確認できます。
理由3)測定点の座標算出に必要な情報を取得するため
必要なのは、加工ワークとタッチプローブが接触している点の座標です。
この接触点の座標を得るためには「計算」が必要です。
理由は、水平面以外だと図のようにタッチプローブの位置と異なるためです。
- 接触時のタッチプローブの「位置(座標)」
- タッチプローブの先端球の「半径(値)」
- 接触点における測定面の「面直方向(ベクトル)」
3次元モデルがあれば、「面直方向」を得ることができます。
4.測定プログラムを作成できるソフトウェアを利用する
測定プログラムの作成には、専用ソフトウェアの利用をおすすめします。
おすすめする理由は3つあります。
理由1)視覚的にわかりやすい
機上測定の専用ソフトウェアは、3次元モデルに対応していることが多いです。
形状を見ながら、3次元モデル上で測定位置を指定できます。
また、タッチプローブを降ろす位置や3次元モデルとの距離、軌道などを画面上で確認できます。
理由2)測定プログラムの安全性が高い
タッチプローブが加工ワークに衝突することは避けなければなりません。
専用ソフトウェアはタッチプローブの軌道を確認できます。
危険を検知できれば、軌道を修正して安全な測定プログラムを作成できます。
奥深い場所を測定する場合は特に注意が必要です。
理由3)測定結果と3次元モデルを比較できる
測定の目的は、加工したワークが設計図通りの寸法になっているか確認することです。
切削加工の場合は、削り残り(または削り過ぎ)の量(=厚み)が重要となります。
この量(=厚み)を測定するには、測定結果の座標と3次元モデルの比較が必要です。
これを助けてくれるのが専用ソフトウェアです。
測定結果の座標から、削り残り(または削り過ぎ)の量を得る方法は2つ考えられます。
- 専用ソフトウェアに測定結果を取り込んで比較する
- 測定プログラム内で比較する
この削り残り(または削り過ぎ)の量を自動で算出したい場合は、上記2が適していると考えられます。
上記1でも自動算出の機能がある専用ソフトであれば可能と考えられます。
弊社は上記2を優先して機上測定用ソフトウェアを開発しました。
このソフトウェアが出力する測定プログラムは、削り残り/過ぎの量を自動で測定できます。
測定の自動化に必要なもの
寸法測定を自動化するために必要なものは以下の6つです。
1.自動測定に対応したタッチプローブが必要
切削加工の原点出しに使用しているタッチプローブを使用します。
原点出しが自動の場合、自動測定が可能です。
原点出しが手動の場合、自動測定は困難です。
加工ワークに接触させる動作を、作業者がダイヤルを回して行っている場合です。
タッチプローブと加工機との間で通信できないため、自動測定が困難です。
自動測定に対応したタッチプローブの導入が必要な場合は?
加工機を購入された機械商社または機械メーカに相談してください。
加工機側に受信機の取り付けと配線が必要であるためです。
なお、機械メーカが推奨しているタッチプローブであれば測定に問題はありません。
2.タッチプローブが使用可能な加工機が必要
タッチプローブが使用可能な加工機であることが重要です。
次のどちらかを満たす加工機が必要です。
- 「G31(スキップ機能)」が使用できる
- 寸法測定の指令が使用できる
FANUC社以外の数値制御(NC)装置では2のように寸法測定機能を搭載している場合があります。
3.加工機側に測定機能(マクロ等)が必要(例外あり)
測定機能=ソフトウェアが必要です。
パターンは3つあります。
- 「搭載されている測定機能」+測定プログラム
- 「寸法測定オプション」+測定プログラム
- 測定プログラムのみ(例外)
上記1のパターンでは、その加工機に対応した測定プログラムを用意するだけで済みます。
上記2は一般的に多いパターンです。
寸法測定オプションがない場合は追加購入が必要です。
追加する際は、加工機の空きメモリ容量にご注意ください。
上記3のパターンは稀です。測定プログラムの中に必要な機能を全て盛り込む必要があるためです。
弊社が販売・サポートしているCimatronの機上測定では、上記の1,2,3の全てに対応しています。
4.機上測定のソフトウェア(PC用)が必要
測定の工程を設計し、測定プログラムを出力できるソフトウェアが必要です。
これはPCにインストールするソフトウェアであることが重要です。
その理由は2つあります。
- 加工機の使用状況に影響を受けない
- 担当を分けて負担を分散できる
PC上で作業するため、加工機の操作は不要です。
また、機械または測定の担当以外の人が測定プログラムを作成することも可能です。
平行して作業できれば、生産効率は向上します。
このソフトウェアの選定は重要です。目的に適したソフトウェアをお選びください。
5.加工機と運用に合わせたカスタマイズが必要
加工機と運用方法に合わせたカスタマイズが必要です。
カスタマイズの詳細については、ソフトウェアメーカまたは販売店に確認してください。
ソフトウェアによって、カスタマイズの範囲は多少異なります。
他のシステムと連携させる場合は、連携できるかを確認する必要があります。
6.加工機とLAN接続されたPC(結果収集用)が必要
測定結果を自動収集したい場合は、加工機とLANで接続されたPCが必要です。
測定結果を収集する方法は2つ考えられます。
- 稼働管理システムを利用して収集
- ファイル送受信ソフトを利用して収集
上記1は加工機内の変数を参照する方法です。
測定プログラムが加工機内の変数に測定結果を書込むためです。
このため稼働管理システムには、加工機の変数を参照できる機能が必要です。
上記2は結果ファイルを収集する方法です。
測定プログラムが測定結果をファイルとして出力できるためです。
結果ファイルを取得するには、ファイル送受信ソフトが必要です。
加工プログラムの送信に利用しているファイル送受信ソフトを利用します。
切削加工~寸法測定までを無人化するポイント
加工機を使って寸法測定を行うわけですから、切削加工から寸法測定までを自動化&無人化したいところです。
そのためのポイントは3つあります。
1.加工と測定のプログラムを連続して実行できるようにする
切削加工と寸法測定を連続して無人運転するためには、各プログラムを連続して実行できる必要があります。
パターンは2つあります。
- 加工スケジュールを管理するシステムに登録する
- メインプログラムを用意する
上記1は、システムに測定プログラムの実行スケジュールを登録するだけで済みます。
上記2は、加工と測定のプログラムを呼び出す「メインプログラム」を作成します。
2.加工機の自動工具交換を利用する
自動工具交換(ATC)装置を利用して切削工具からタッチプローブに自動で交換させる必要があります。
手動で工具を取り付ける方法では、人による作業が必要になってしまうためです。
3.削りカス(切粉)と切削油を取り除く工夫をする
寸法測定する前に、加工ワークをきれいに洗浄する必要があります。
何故なら、切削加工後の加工ワークには切粉(キリコ)と呼ばれる削りカスと切削油または切削剤が付着しているからです。
加工~測定までを自動化するためには、洗浄を自動化する必要があります。
洗浄を自動化するためのアイデアは2つあります。
アイデア1)エアーで吹き飛ばす
加工機のエアーノズルからエアーを強く吹き付ける方法があります。
測定する前に、測定箇所付近の切粉や切削油/剤をエアーで吹き飛ばします。
これはプログラムで実現可能です。
ただし、凹形状部に堆積した切粉などの洗浄は、エアーを吹き付ける時間を長めにするなどの工夫が必要です。
アイデア2)切粉を小さくする
荒加工の切粉は1つ1つが大きくなりがちです。
なるべく切粉を小さくすることで、エアーで吹き飛ばしやすくなります。
荒加工の切粉をエアーで吹き飛ばすのが困難な場合は、切粉が小さくなる荒加工専用の切削工具がおすすめです。
高送りに対応した工具であれば、荒加工時間の短縮にもなります。
複数のワークに対して連続自動運転するポイント
加工→測定までを複数のワークに対して連続で行う場合は、それなりの工夫が必要です。
その方法は大きく2つ考えられます。
1.機械テーブルに複数のワークを配置して連続運転する
加工するワークを加工機のテーブル上に複数配置する方法です。
加工原点を切り替えて連続運転します。
ワークを機械テーブルに固定する方法は2つあります。
- マシンバイスでワークを固定する
- テーブルに直接固定する
上記1はワークが小さい場合によく使われる方法です。
マシンバイスと呼ばれる固定ツールを使います。
マシンバイスを機械テーブルに固定し、そのマシンバイスにワークを固定します。
マシンバイスを常に固定しておくことで、短時間でワークを固定できます。
上記2はマシンバイスでは固定できない大きさのワークに用いる方法です。
クランプと呼ばれる治具でワークをテーブルに固定します。
いずれも各ワークの加工原点出しを事前に終えておくことが重要です。
2.自動ワーク交換装置を利用して連続運転する
自動ワーク交換装置(ワークチェンジャー)を利用する方法があります。
自動パレットチェンジャーと呼ばれる装置もあります。
この方法で自動運転&無人運転を行っている事例があります。
加工機による寸法測定では困難なこと
加工機を使った寸法測定では困難なことがあります。
1.タッチプローブが届かないところは測定ができない
タッチプローブの先端球(プローブ球)の大きさと軸の長さでは測定したい箇所に届かない場合があります。
先端のプローブ球を小さいサイズに交換することで、測定が可能になる場合があります。
また軸を長いものに交換することで、測定が可能になる場合もあります。
それでも届かない箇所は測定ができません。
2.手動タイプのタッチプローブでは自動測定ができない
手動タイプのタッチプローブでは自動測定ができません。
何故なら担当者の操作が必要になるためです。
タッチプローブの移動は手動です。ワークとタッチプローブの接触は、ランプや音で判断します。
自動測定のためには、自動タイプのタッチプローブが必要です。
まとめ
従来のように3次元測定機を使った寸法測定では、自動測定を実現することは簡単ではありません。
加工機を測定機代わりにすることができれば、寸法測定が自動化できます。更に加工~測定までを自動&無人化できる可能性もあります。
是非一度、ご検討されてはいかがでしょうか?
加工機で寸法測定する「機上測定」を導入することで、寸法測定が自動化できます。
この記事が参考になれば幸いです。
Cimatronをお使いの方へ
弊社が販売・サポートしている統合3次元CAD/CAMシステムCimatronには機上測定のオプションがあります。
弊社ホームページに紹介ページがありますので、ぜひご覧ください。
この下にあるリンクをクリックすると紹介ページをご覧いただけます。
関連する記事
Cimatron課の戸村です。
加工したワークの寸法測定でお困りではありませんか?
特に金型製造において、寸法測定を自動化することは簡単ではないと聞きます。
金型部品には勾配のついた面や曲面をもつ部品があるためです。
また各部品の加工数は1~数個と少なく、部品の種類が多いことも自動化が難しい要因と考えられます。
実は加工機を測定機代わりにすることによって、寸法測定を自動化&無人化できる方法があります。
ここでは、加工機を使った寸法測定を自動化するポイントや必要なものなどについて説明します。
これからご説明する内容は、以下に該当される方を対象としています。
- 様々な形状の部品を少ない数だけ加工されている(金型製造など)
- 自動工具交換(ATC)装置と数値制御(NC)が付いたミーリング加工機を使用している
いわゆるマシニングセンターです。NCフライス盤、NC旋盤は対象外です。
- タッチプローブで加工素材の原点出しをされている
加工されたワークを加工機上に置いたまま寸法測定することを「機上測定」と言います。
加工機を測定機代わりに利用することで、自動測定が可能となります。
機上測定&自動測定によって、無人運転が可能となります。
切削加工~寸法測定までを自動化&無人化することで、作業者の負担を軽減でき、工数とコストが削減できます。
目次
加工ワークの寸法測定を自動化するポイント
1.加工機を測定機にする(機上測定)
マシニングセンターと呼ばれるミーリング加工機は、測定機代わりにすることが可能です。
ただし、加工機の仕様上できない場合があります。
測定機代わりにできる理由は3つあります。
理由1)3次元測定機と同様のタッチセンサーが使える(タッチプローブ)
加工機用のタッチプローブが使用できます。
このタッチプローブは、3次元測定機で使われているタッチプローブと同様のタッチセンサーです。
理由2)3次元測定機と加工機の構造が類似している
3次元測定機と加工機のハードウェアを比較すると、その構成要素はかなり似ています。
どちらも同様の構成要素を持っています。
- 駆動軸(X軸、Y軸、Z軸)
- タッチセンサー(タッチプローブ)
理由3)ソフトウェアの違いを補える
3次元測定機と加工機の大きな違いは測定機能です。つまりソフトウェアの違いです。
加工機は測定機能が不足しています。これは「測定プログラム」で補うことができます。
加工機の測定プログラムは、加工機が認識できるプログラムコードで記述します。
2.測定対象の加工ワークを動かさない
自動化には人が関わる「作業」を取り除くことが必要です。その一つが測定のための「ワーク移動」です。
このワーク移動を取り除く方法は2つ考えられます。
- 自動化できる設備を導入する(ロボットアーム+自動搬送装置など)
- 加工機上で寸法測定する
加工機上で寸法測定ができれば、ワークの移動が不要となります。(上記2)
更に追加工時のワーク移動も不要となります。
また、次の作業も不要となります。
- 3次元測定機上での原点出し作業
- 追加工での原点出し作業
いずれも人が関わる「作業」です。
3.3次元のモデルデータを利用する
勾配面や曲面のある加工ワークを測定するために、3次元モデルが必要です。
一般的にはソリッドモデルが適しています。サーフェイスモデルでも可能です。
3次元モデルが必要な理由は3つあります。
理由1)接触するタッチプローブの位置を取得するため
タッチプローブの先端は球になっています。
そのため、測定したい点にタッチプローブの先端球を正確に接触させる必要があります。
この時のタッチプローブの位置を得るために、3次元モデルが必要です。
理由2)タッチプローブの安全な位置や軌道を確認するため
タッチプローブが安全な軌道を通るかどうかを確認するために、加工ワークの3次元モデルが必要です。
タッチプローブの軌道と、加工ワークとの位置関係を確認できます。
理由3)測定点の座標算出に必要な情報を取得するため
必要なのは、加工ワークとタッチプローブが接触している点の座標です。
この接触点の座標を得るためには「計算」が必要です。
理由は、水平面以外だと図のようにタッチプローブの位置と異なるためです。
- 接触時のタッチプローブの「位置(座標)」
- タッチプローブの先端球の「半径(値)」
- 接触点における測定面の「面直方向(ベクトル)」
3次元モデルがあれば、「面直方向」を得ることができます。
4.測定プログラムを作成できるソフトウェアを利用する
測定プログラムの作成には、専用ソフトウェアの利用をおすすめします。
おすすめする理由は3つあります。
理由1)視覚的にわかりやすい
機上測定の専用ソフトウェアは、3次元モデルに対応していることが多いです。
形状を見ながら、3次元モデル上で測定位置を指定できます。
また、タッチプローブを降ろす位置や3次元モデルとの距離、軌道などを画面上で確認できます。
理由2)測定プログラムの安全性が高い
タッチプローブが加工ワークに衝突することは避けなければなりません。
専用ソフトウェアはタッチプローブの軌道を確認できます。
危険を検知できれば、軌道を修正して安全な測定プログラムを作成できます。
奥深い場所を測定する場合は特に注意が必要です。
理由3)測定結果と3次元モデルを比較できる
測定の目的は、加工したワークが設計図通りの寸法になっているか確認することです。
切削加工の場合は、削り残り(または削り過ぎ)の量(=厚み)が重要となります。
この量(=厚み)を測定するには、測定結果の座標と3次元モデルの比較が必要です。
これを助けてくれるのが専用ソフトウェアです。
測定結果の座標から、削り残り(または削り過ぎ)の量を得る方法は2つ考えられます。
- 専用ソフトウェアに測定結果を取り込んで比較する
- 測定プログラム内で比較する
この削り残り(または削り過ぎ)の量を自動で算出したい場合は、上記2が適していると考えられます。
上記1でも自動算出の機能がある専用ソフトであれば可能と考えられます。
弊社は上記2を優先して機上測定用ソフトウェアを開発しました。
このソフトウェアが出力する測定プログラムは、削り残り/過ぎの量を自動で測定できます。
測定の自動化に必要なもの
寸法測定を自動化するために必要なものは以下の6つです。
1.自動測定に対応したタッチプローブが必要
切削加工の原点出しに使用しているタッチプローブを使用します。
原点出しが自動の場合、自動測定が可能です。
原点出しが手動の場合、自動測定は困難です。
加工ワークに接触させる動作を、作業者がダイヤルを回して行っている場合です。
タッチプローブと加工機との間で通信できないため、自動測定が困難です。
自動測定に対応したタッチプローブの導入が必要な場合は?
加工機を購入された機械商社または機械メーカに相談してください。
加工機側に受信機の取り付けと配線が必要であるためです。
なお、機械メーカが推奨しているタッチプローブであれば測定に問題はありません。
2.タッチプローブが使用可能な加工機が必要
タッチプローブが使用可能な加工機であることが重要です。
次のどちらかを満たす加工機が必要です。
- 「G31(スキップ機能)」が使用できる
- 寸法測定の指令が使用できる
FANUC社以外の数値制御(NC)装置では2のように寸法測定機能を搭載している場合があります。
3.加工機側に測定機能(マクロ等)が必要(例外あり)
測定機能=ソフトウェアが必要です。
パターンは3つあります。
- 「搭載されている測定機能」+測定プログラム
- 「寸法測定オプション」+測定プログラム
- 測定プログラムのみ(例外)
上記1のパターンでは、その加工機に対応した測定プログラムを用意するだけで済みます。
上記2は一般的に多いパターンです。
寸法測定オプションがない場合は追加購入が必要です。
追加する際は、加工機の空きメモリ容量にご注意ください。
上記3のパターンは稀です。測定プログラムの中に必要な機能を全て盛り込む必要があるためです。
弊社が販売・サポートしているCimatronの機上測定では、上記の1,2,3の全てに対応しています。
4.機上測定のソフトウェア(PC用)が必要
測定の工程を設計し、測定プログラムを出力できるソフトウェアが必要です。
これはPCにインストールするソフトウェアであることが重要です。
その理由は2つあります。
- 加工機の使用状況に影響を受けない
- 担当を分けて負担を分散できる
PC上で作業するため、加工機の操作は不要です。
また、機械または測定の担当以外の人が測定プログラムを作成することも可能です。
平行して作業できれば、生産効率は向上します。
このソフトウェアの選定は重要です。目的に適したソフトウェアをお選びください。
5.加工機と運用に合わせたカスタマイズが必要
加工機と運用方法に合わせたカスタマイズが必要です。
カスタマイズの詳細については、ソフトウェアメーカまたは販売店に確認してください。
ソフトウェアによって、カスタマイズの範囲は多少異なります。
他のシステムと連携させる場合は、連携できるかを確認する必要があります。
6.加工機とLAN接続されたPC(結果収集用)が必要
測定結果を自動収集したい場合は、加工機とLANで接続されたPCが必要です。
測定結果を収集する方法は2つ考えられます。
- 稼働管理システムを利用して収集
- ファイル送受信ソフトを利用して収集
上記1は加工機内の変数を参照する方法です。
測定プログラムが加工機内の変数に測定結果を書込むためです。
このため稼働管理システムには、加工機の変数を参照できる機能が必要です。
上記2は結果ファイルを収集する方法です。
測定プログラムが測定結果をファイルとして出力できるためです。
結果ファイルを取得するには、ファイル送受信ソフトが必要です。
加工プログラムの送信に利用しているファイル送受信ソフトを利用します。
切削加工~寸法測定までを無人化するポイント
加工機を使って寸法測定を行うわけですから、切削加工から寸法測定までを自動化&無人化したいところです。
そのためのポイントは3つあります。
1.加工と測定のプログラムを連続して実行できるようにする
切削加工と寸法測定を連続して無人運転するためには、各プログラムを連続して実行できる必要があります。
パターンは2つあります。
- 加工スケジュールを管理するシステムに登録する
- メインプログラムを用意する
上記1は、システムに測定プログラムの実行スケジュールを登録するだけで済みます。
上記2は、加工と測定のプログラムを呼び出す「メインプログラム」を作成します。
2.加工機の自動工具交換を利用する
自動工具交換(ATC)装置を利用して切削工具からタッチプローブに自動で交換させる必要があります。
手動で工具を取り付ける方法では、人による作業が必要になってしまうためです。
3.削りカス(切粉)と切削油を取り除く工夫をする
寸法測定する前に、加工ワークをきれいに洗浄する必要があります。
何故なら、切削加工後の加工ワークには切粉(キリコ)と呼ばれる削りカスと切削油または切削剤が付着しているからです。
加工~測定までを自動化するためには、洗浄を自動化する必要があります。
洗浄を自動化するためのアイデアは2つあります。
アイデア1)エアーで吹き飛ばす
加工機のエアーノズルからエアーを強く吹き付ける方法があります。
測定する前に、測定箇所付近の切粉や切削油/剤をエアーで吹き飛ばします。
これはプログラムで実現可能です。
ただし、凹形状部に堆積した切粉などの洗浄は、エアーを吹き付ける時間を長めにするなどの工夫が必要です。
アイデア2)切粉を小さくする
荒加工の切粉は1つ1つが大きくなりがちです。
なるべく切粉を小さくすることで、エアーで吹き飛ばしやすくなります。
荒加工の切粉をエアーで吹き飛ばすのが困難な場合は、切粉が小さくなる荒加工専用の切削工具がおすすめです。
高送りに対応した工具であれば、荒加工時間の短縮にもなります。
複数のワークに対して連続自動運転するポイント
加工→測定までを複数のワークに対して連続で行う場合は、それなりの工夫が必要です。
その方法は大きく2つ考えられます。
1.機械テーブルに複数のワークを配置して連続運転する
加工するワークを加工機のテーブル上に複数配置する方法です。
加工原点を切り替えて連続運転します。
ワークを機械テーブルに固定する方法は2つあります。
- マシンバイスでワークを固定する
- テーブルに直接固定する
上記1はワークが小さい場合によく使われる方法です。
マシンバイスと呼ばれる固定ツールを使います。
マシンバイスを機械テーブルに固定し、そのマシンバイスにワークを固定します。
マシンバイスを常に固定しておくことで、短時間でワークを固定できます。
上記2はマシンバイスでは固定できない大きさのワークに用いる方法です。
クランプと呼ばれる治具でワークをテーブルに固定します。
いずれも各ワークの加工原点出しを事前に終えておくことが重要です。
2.自動ワーク交換装置を利用して連続運転する
自動ワーク交換装置(ワークチェンジャー)を利用する方法があります。
自動パレットチェンジャーと呼ばれる装置もあります。
この方法で自動運転&無人運転を行っている事例があります。
加工機による寸法測定では困難なこと
加工機を使った寸法測定では困難なことがあります。
1.タッチプローブが届かないところは測定ができない
タッチプローブの先端球(プローブ球)の大きさと軸の長さでは測定したい箇所に届かない場合があります。
先端のプローブ球を小さいサイズに交換することで、測定が可能になる場合があります。
また軸を長いものに交換することで、測定が可能になる場合もあります。
それでも届かない箇所は測定ができません。
2.手動タイプのタッチプローブでは自動測定ができない
手動タイプのタッチプローブでは自動測定ができません。
何故なら担当者の操作が必要になるためです。
タッチプローブの移動は手動です。ワークとタッチプローブの接触は、ランプや音で判断します。
自動測定のためには、自動タイプのタッチプローブが必要です。
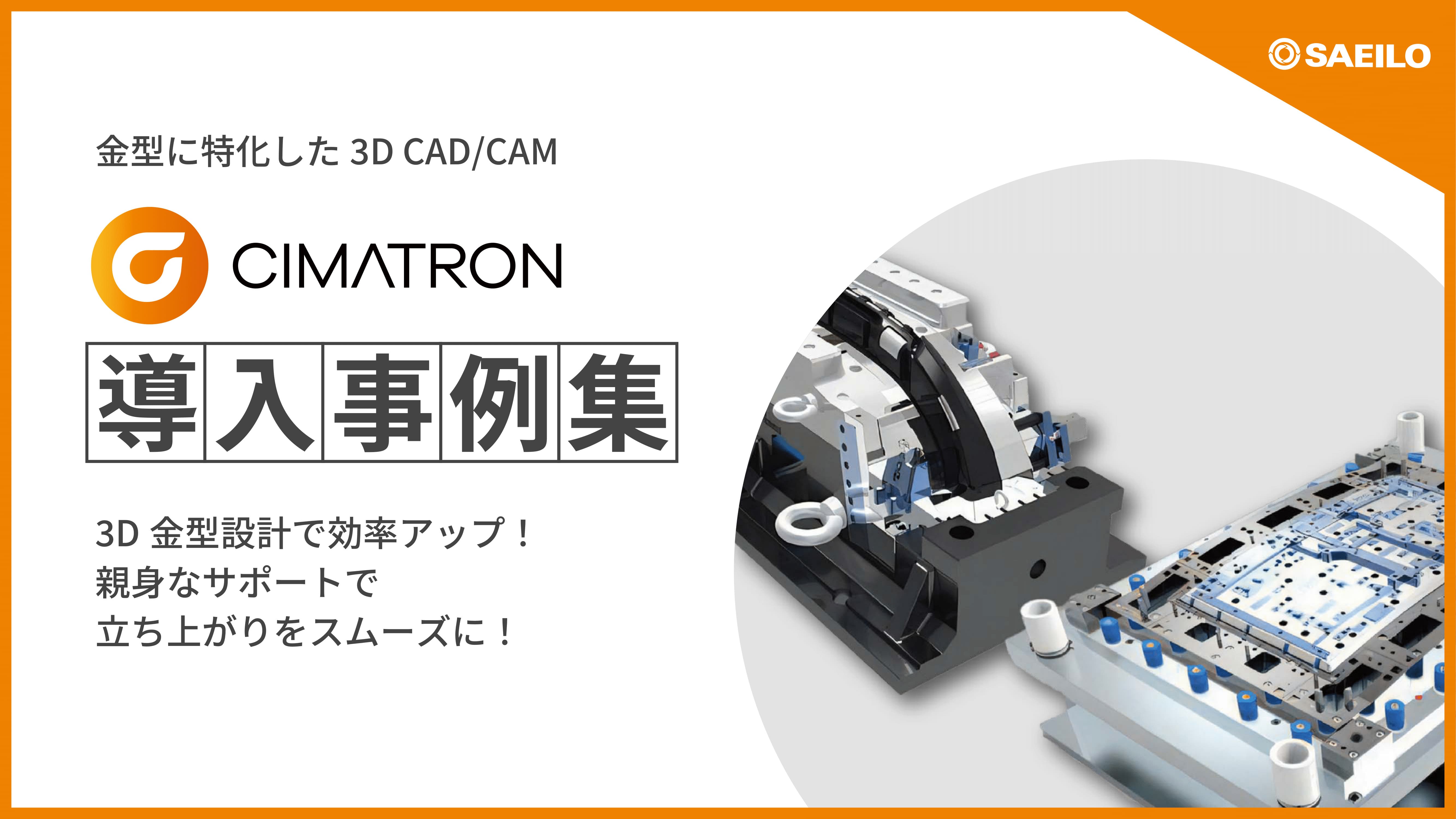
まとめ
従来のように3次元測定機を使った寸法測定では、自動測定を実現することは簡単ではありません。
加工機を測定機代わりにすることができれば、寸法測定が自動化できます。更に加工~測定までを自動&無人化できる可能性もあります。
是非一度、ご検討されてはいかがでしょうか?
加工機で寸法測定する「機上測定」を導入することで、寸法測定が自動化できます。
この記事が参考になれば幸いです。
Cimatronをお使いの方へ
弊社が販売・サポートしている統合3次元CAD/CAMシステムCimatronには機上測定のオプションがあります。
弊社ホームページに紹介ページがありますので、ぜひご覧ください。
この下にあるリンクをクリックすると紹介ページをご覧いただけます。