加工パス間隔と表面粗さ ~粗さ記号とパス間隔との関係~
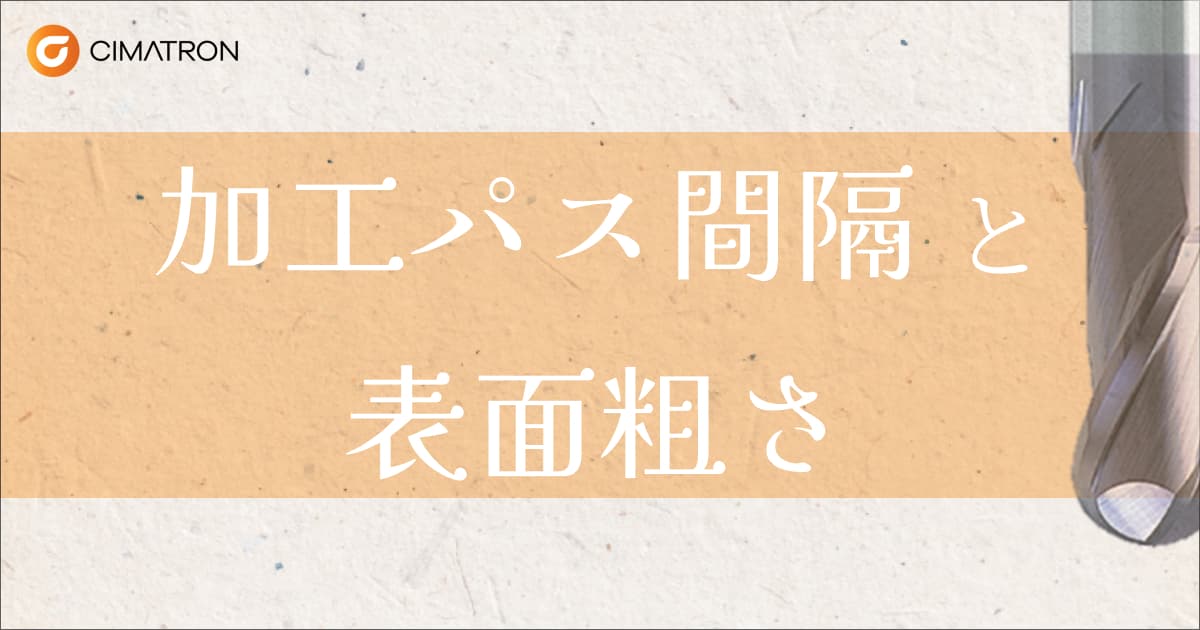
CAMの設定と表面荒さ
プラスチック金型やプレス金型、鍛造金型、鋳造金型の製造において、3次元CAMを利用した場合の加工面荒さと加工パスのピッチとの関連に関してご紹介します。多少なりともご参考になれば幸いです。これからご説明する内容は、以下に該当する方を対象としています。ぜひ、ご覧ください。
- 工具Rの大きさと面粗さの関係を確認したい方
- CAMでパス間ピッチを設定するのに迷っている方
- 図面にある精度記号と加工についての関係を確認したい方
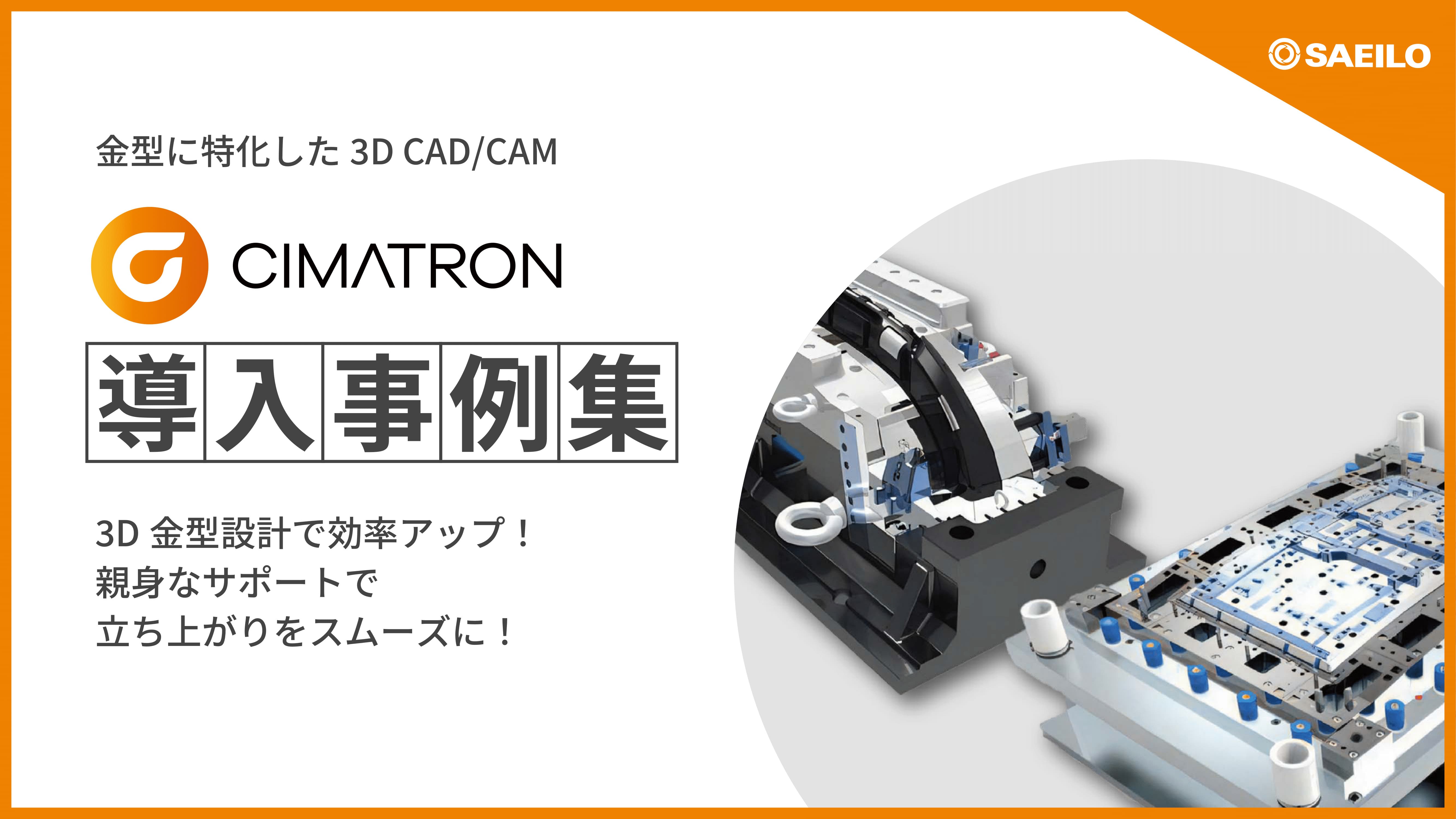
目次
表面粗さとは
表面粗さとは何でしょうか?加工物の加工面の状態を凹凸という観点から表した言葉です。よく、ピカピカしているとかざらざらしているなどと面の状態を言葉で表すことがあります。その状態を誰でも判断できる工業的な数値で表したものを表面粗さと言います。
2次元と3次元の表面粗さ
粗さを測定する場合に一般的には表面を線上にトレースして測定する線粗さと光学的な手法で広範囲な面を測定する面粗さがあります。
線粗さ:面の一部の断面線をトレースする方法で測定
面粗さ:3次元的な非接触測定器で面を測定
長年にわたり線粗さが表面粗さとして使用されており、利用実績と信頼性があります。今後も粗さの主流として使い続けられると思われます。しかし、面の一部のある方向のみを測定する線粗さより、面全体を評価でき異方性も評価できる面粗さのほうがより正確に面の状態を捉えることができるので、面粗さを使用する場面は増えていく事が考えられます。(測定器の価格が高かったり、測定時間が長かったりする問題はありますが.....)
表面粗さの種類(線粗さ)
表面粗さを表す値には下記のものがあります。
線粗さ
- Ra 算術平均粗さ
- Rz 最大高さ粗さ
- Rzjis 十点平均粗さ
これらは面の一部の断面をトレースする方法で測定されます。
Ra
Ra:基準長さにおいて中心線からの高さと深さの絶対値の平均で表します。傷やゴミ、ノイズなどの突発的な変化の影響を受けにくい数値です。一般的によく使用される値です。
Rz
Rz:基準長さの中で最大の山高さと谷深さの間の距離 よく使用される値ですが、最大値を使用するので様々なノイズの影響を受けてしまう点に注意が必要です。
Rzjis(十点平均粗さ)
Rzjis:山、谷の最高値5点ずつの平均を合わせた値。Rzの名前で旧JIS規格にあり広く使用されていた。ISOからは削除されたため、国内用にRzjisという名前で残り、使われている。(新JIS規格のRzと混同しないように注意)
切削加工における表面粗さ
マシニングセンタなどで回転工具(ボールエンドミル)を使用した切削加工の場合、表面粗さに関係する加工要素は2点あります。
- パス間ピッチ:工具が通る間隔。通る間に加工されない山が残りその高さをスカラップハイトと呼ぶ
- 断続切削による刃の切削形状:刃が材料を切削して次の刃が来るまで工具が移動しているため、削られない部分が発生する
ピッチによるスカラップハイト
工具と工具の通路の間の削り残し高さをスカラップハイトと言います。 このスカラップハイトは計算によって求めることが可能です。
$$h = r \times \left[ 1 - \cos \left( \sin^{-1} \left(\frac{p}{2r}\right) \right) \right]$$
しかし、これでは計算が難しいので
$$h \ll r$$
の場合に簡易的に
$$h = \frac{p^2}{8r}$$
で計算できます。
スカラップハイトと表面粗さ
ピッチと工具半径でカスプハイトが出ます。このカスプハイトは、表面粗さで言えばRzの値に相当します。ボール工具の場合、h< 一般的には仕上げとこのRaの関係は下記のようになっているようです。
表面粗さ (Ra) | 範囲 | 仕上げ方法 | 記号 |
---|---|---|---|
Ra | ~0.2 | 研磨鏡面仕上げ | ▽ ▽ ▽ ▽ |
Ra | 0.4 ~ 1.6 | 切削/研磨 仕上げ | ▽ ▽ ▽ |
Ra | 3.2 ~ 6.3 | 切削仕上げ | ▽▽ |
Ra | 12.5 ~ 25 | 切削粗仕上げ | ▽ |
昔は▽記号しかなく、状態を言葉で表現することもありましたが、現在は数値で指定されるので明確ですね。
仕上げとピッチ
実際の工具Rとピッチでどの程度のRaになるのかを表にしました。黄色と紫の間であれば ▽ ▽ ▽ 程度の仕上げになります。とはいえ範囲の右と左ではRaで8~10倍近く差があり、仕上げ状態に差があります。
実際の加工画像
マシニングセンタで実際に加工し測定してみました。機械、工具の精度の影響などで理論値より大きなRaの値となりました。③と④の見た目に変化ほとんどなく、ピッチをいくら小さくしても面粗さの限界があることが分かります。
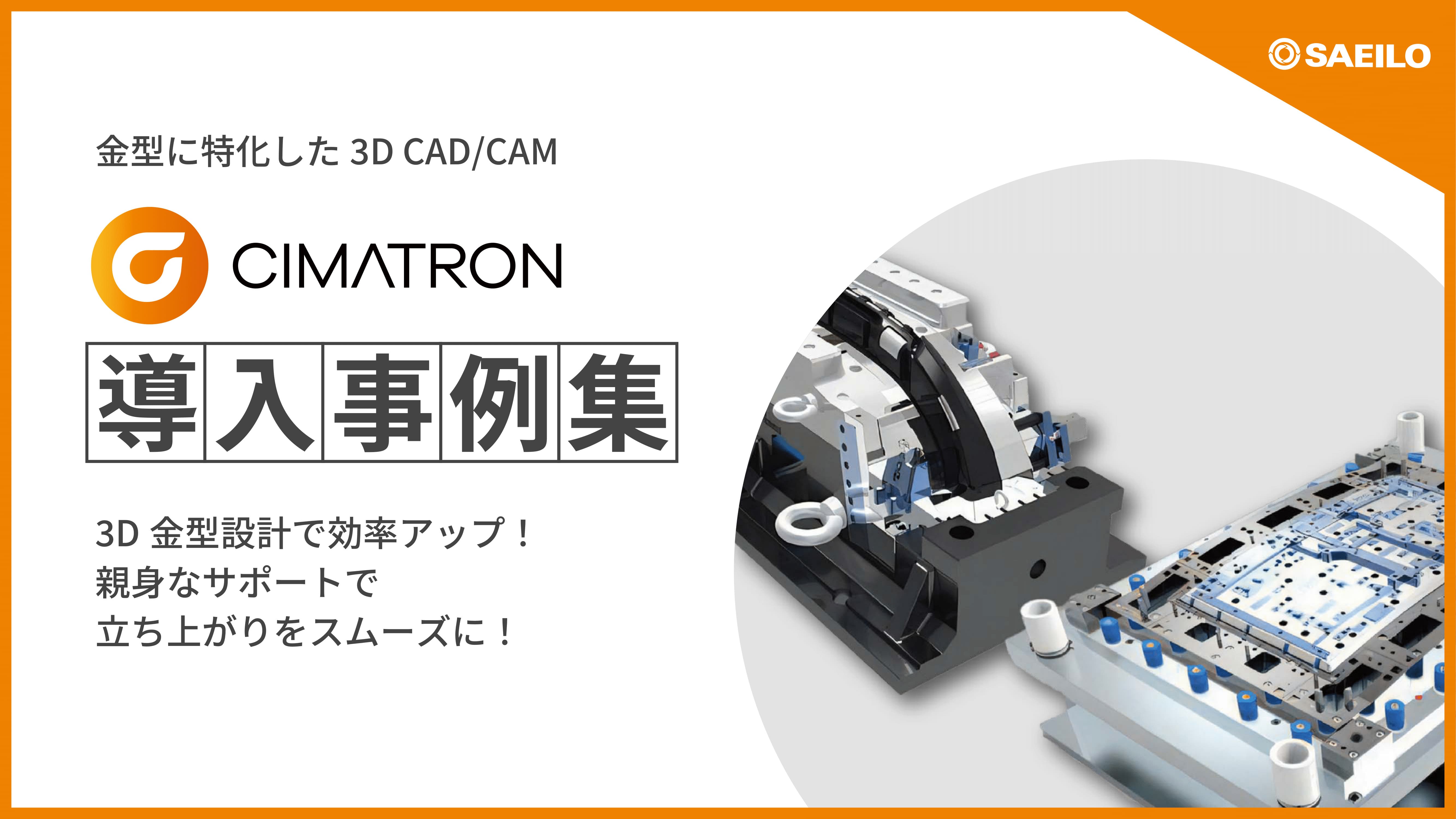
結論
現在の仕上げ記号はRa、Rzなどで指定されています。その数値からステップ、ピック値などを計算してその値を入力することで必要な面粗さを実現することが可能です。もちろんRaのこの値は、この工具ではピッチはこれくらいという経験値はお持ちの方も多いとは思います。ですが、一度使用しているピッチや工具RなどからRaを計算してみてはいかがでしょうか?過剰な仕上げや逆に面粗さが不十分であったりすることをチェックできます。繰り返しにはなりますが、工具半径(r)に対してスカラップハイト(h)が十分小さい場合にはピッチ(p)を用いて簡易的にhを計算できます。
$$h = \frac{p^2}{8r}$$
活用頂ければ幸いです。
(但し、これは平面を基準としています。曲面の場合は次のブログで考察したいと思います。)
ここまでお読みくださり、ありがとうございました。
セイロジャパンでは、プラスチック金型やプレス金型用に特化したCAD/CAM「Cimatron」を取り扱っております。
関心をお持ちいただけましたら、下記フォームよりお気軽にお問い合わせください。