東陽実業による車用フォグランプの外観不良対策事例
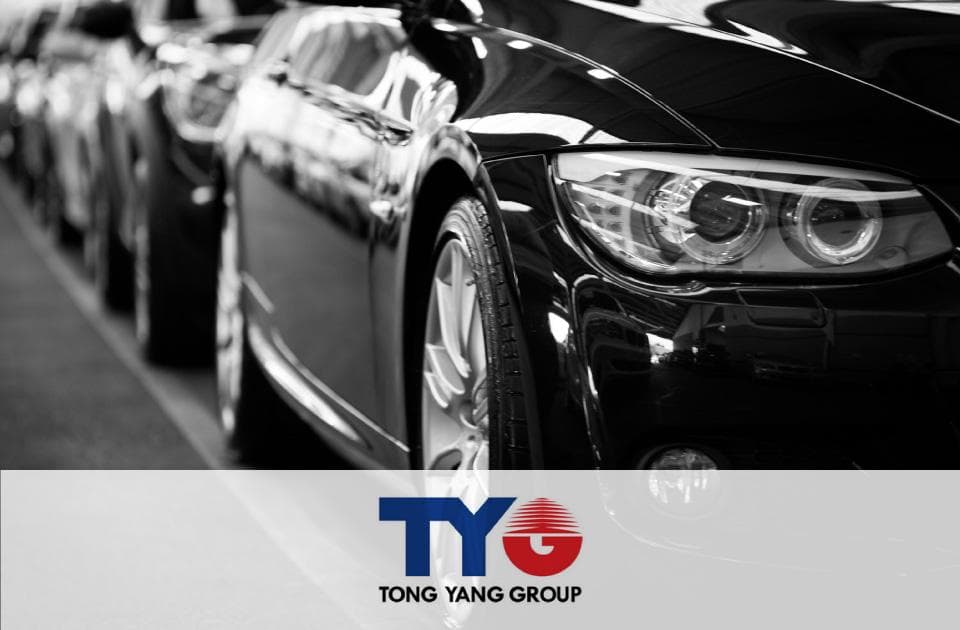
顧客情報
東陽実業グループは、世界最大の自動車衝突部位部品メーカーとして、50年余りかけて蓄積してきた豊富な専門技術力、販売力およびグローバル経営力をもって業界をリードしています。
- 顧客名:東陽実業
- 国名:台湾
- 産業:自動車
- 導入ソリューション:Moldex3D Advancedソリューション、樹脂流動解析Flow
目次
1.概要:肉厚調整による外観品質の改善
本事例では樹脂射出成形によって製造される車用フォグランプ部品(図1)に生じた、外観上の欠陥(図2)の問題をとりあげます。本事例が対象とする製品は自動車内装の外観部品のため、表面にウェルドラインが出ないようにする必要があります。また、ドアロック部品においても、外観表面上でのウェルドライン発生を防止する必要があります。東陽社は、Moldex3Dの樹脂流動解析を用いて、ゲートレイアウトがウェルドラインの位置および会合角に及ぼす影響を検証し、改善を行った結果、肉厚を調整することによってキャビティのエアトラップ問題と、製品の外観品質を改善しました。
図1 本事例が対象とするフォグランプ部品
図2 青色で示した部分が顕著な外観問題が見られた箇所
2.製品の2つの課題
- 製品外観のウェルドラインの防止
- 効果的な最適設計によるエアトラップ問題の解決
3.導入ソリューション:エアトラップおよびウェルドライン位置の改善
東陽社は、ランナーレイアウトと肉厚を変えて解析を行い、流動挙動を最適化し、製品外観のウェルドラインを防止しました。そのほか、Moldex3Dの流動解析結果に基づいて角部分の肉厚の調整を行い、エアトラップおよびウェルドラインの位置も改善しました。
4.ケーススタディ:ゲートタイプの違いによる検証
本事例が対象とする車用フォグランプ製品の研究開発は、設計段階と試作段階に分かれています。各段階での目的に合わせてMoldex3Dの解析技術を応用します。金型製作前の設計段階においては、ゲート設計の検証および潜在的な外観不具合を予測するために解析を行います。ゲート設計においてはゲート数、ゲート位置およびランナーレイアウトを変化させた3つのゲートタイプについて検証を行います。設計決定は完成品のウェルドラインおよびエアトラップの数量を基準としており、外観不具合が最も少ない設計が、最適化の程度が最も高い製品であるとみなします。金型を製作して最初の試作を行った後、解析技術を用いて実際の試作成形品の検証を行います。そのほか、試作成形品で生じた不具合を解析し、その不具合が生じる根本的な原因と、有効な解決策を見出します(図3)。
図3 研究開発の各段階における主な目標
Moldex3Dでまず初めにゲート設計の検証を行います。図4に示すとおり、Type Aの設計においては製品の下方中央にシングルゲートがあります。Type Bもシングルゲートですが、ゲート位置を下方右側に変更しています。Type Cは左右両側にゲートが1つずつあります。すべての設計の解析を終えた後、さらにウェルドラインおよびエアトラップが目立つ場所に現れていないかを観察して最終設計の参考とします。
図4 製品外観の品質要件および3タイプのゲート設計
図5の比較表のとおり、Type Bのウェルドラインおよびエアトラップの問題が最も軽微であることがわかります。そのため、この設計を外観の最適化の程度が最も高い設計選択とみなします。
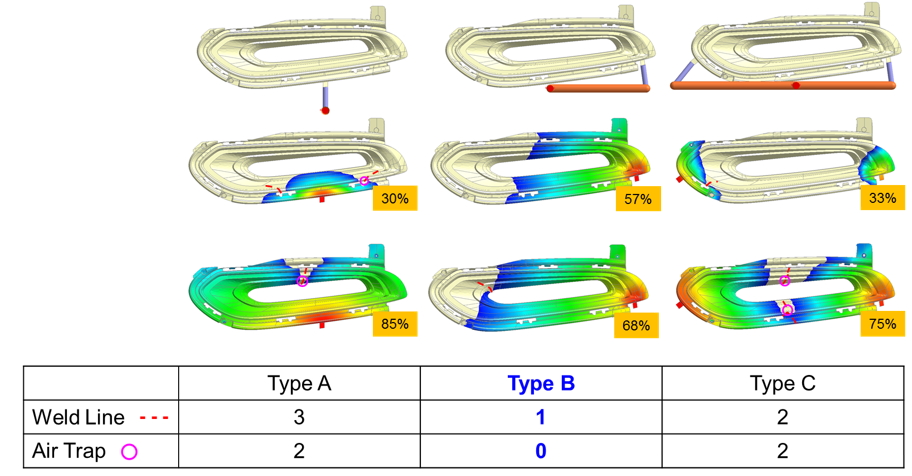
図5 3タイプのゲート設計解析結果の比較
通常ウェルドライン品質を評価する際は、ウェルドラインの会合角を判断材料にします。当初の肉厚設計におけるウェルドライン会合角は約120度でしたが、肉厚設計の最適化によりウェルドライン会合角が140度に改善しました(図6)。これはウェルドラインが短くなり、目立たなくなったことを意味しています。
図6 製品肉厚の最適化によってウェルドライン品質が改善
金型を製造して最初の試作を行った後、実際の試作成形品を用いて解析結果の検証を行いました。図7の充填割合の異なる図および写真が示すとおり、解析結果と実際の試作成形品におけるショートショット状態はほぼ一致しています。
図7 充填状態の比較
しかし、最初の試作においても製品表面にエアトラップ現象が生じました。このエアトラップはキャビティ側に現れ、エアベントによって排除することはできません。充填解析は、角部分の流動が周囲よりも早いことを示しており、試作結果と一致しています。根本的な原因は、面取りされた形状によって当該箇所の肉厚(3.5 mm)が製品のほかの部分の肉厚(2.5 mm)よりも厚くなっているため、より厚みのある部分は抵抗が小さくなり、樹脂の流れが速くなることにあります。 そのため、東陽社は、肉厚が3.5 mmの箇所にコアアウトを設ける解決策を考案し、Moldex3Dを利用してその検証を行いました(図8)。コアアウト箇所のメルトフロント結果は図9に示すとおりであり、この設計変更によってウェルドラインが2本増えますが、表からは見えない位置に発生しているため、設計の許容範囲内となります。
図8 不具合予測解析および解決策
図9 製品にコアアウトを設けた後の充填解析
次に、新たにコアアウトを設けた設計を用いて金型の修正を行い、試作後に再度エアトラップおよびウェルドラインの問題について確認を行ったところ、試作結果は解析結果と一致しました。そのため、肉厚が厚い箇所にコアアウトを設けた設計により、エアトラップ問題は解決しました。新たに発生した別のウェルドラインについても見えない箇所にあるため、許容範囲内として扱います(図10)。
図10 対策案の設計変更および検証
5.成果と結論
今回、Moldex3Dを使用することで、以下の結果を確認できました。
1.ウェルドラインおよびエアトラップがもたらす製品の外観不具合を効果的に解決
2.度重なる金型修正によって生じるコストの回避
3.設計期間の短縮
本事例は下記URLよりMoldex3Dの開発元であるコアテックシステム社の記事を参照しています。
https://jp.moldex3d.com/blog/customer_success/the-method-to-improve-surface-quality-of-automotive-fog-lamp-bezels/
ここまでお読みいただきありがとうございました。