株式会社寿原テクノス様【鋳造金型メーカー】モデリング時間の短縮
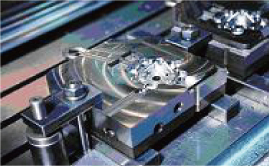
金型設計(モールドデザイン)導入で設計・製作効率アップ
名古屋駅から車で30分ほどの愛知県稲沢市に株式会社原テクノスが新工場を建築したのは、2006年6月のことであった。ダイカスト金型を製造する同社は、芸術的な分野とされてきた金型製作をCAD/CAMの積極的な導入により「芸術域から技術域へ」と変貌させ、金型の精度信頼性を向上させてきた。(当社のパンフレットより)
まだ新しい工場の中は、確かに隅々まで整然と整備され、生産管理ソフトで工程管理を行うなど、随所に管理が行き届いていることを感じされられた。
豊富な加工ノウハウで海外でも高い競争力
寿原テクノスは、主に自動車関係のアルミダイカスト金型(平均800トンクラスから最大2500トンまで)を製作している。北米や東南アジアなどからの受注もある。当社は、かねてより海外との厳しい競争に対抗できる体質作りを進めてきた。
「人件費の高い日本メーカーが競争力を高めるには、工数削減が一番のポイントです。」 (製造部部長 伊藤孝昭氏)との観点から、さまざまな合理化が行われている。たとえば、金型製品部分の加工は、自社開発のクランプシステムを使って黒皮の四角い材料を歪んだままで加工させ、通常5工程かかるところを2工程に集約し、リードタイム短縮と低減につなげている。このとき、特殊なジグを使用し、重切削でも動がないことをテスターで確認してつかみ代を設定するなど、合理的理論的な検証を行っている。
また、放電加工は減らし、なるべく切削加工する方針であり、高硬度材の加工ノウハウ蓄積にも力を注いでいる。他社でできなかった高硬度材(HRC48-50)の直彫り加工を依頼されこともあったが、「HRC50の材料では、アスペクト比20Dの工具まで使っています。」(伊藤部長)と彫り加工のノウハウも豊富であり、工具の研磨部を抱えているので、三分の一の工具代で納めることができたという。
シフト制はしいていないが、マシニングセンタの月間稼働時間は、600時間から720時間に上り、フル稼働状態である。
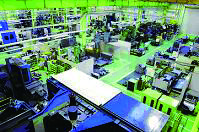
工場内部
2006年Cimatronを導入
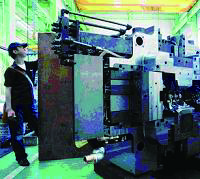
寿原テクノスがCimatronを導入したのは、2006年のことであった。従来使用していたCAMシステムでは、増加する仕事量に対応できず、十数名のCAD/CAM部隊の人員を増やさずにデータ供給能力を高めることが目的であった。
特に人のかかわる時間を短縮するため、全体作業時間の80%を占めるモデリング時間の 短縮を重視した。主要な数社のシステムを検討し、その他、バス計算時間、バスや加工面の品質、電極機能なども総合的に判断してCimatronを選択した。
旧シリーズのΦSTATION が金型分野で定評があったこと、サポート体制がしっかりしていることも選定の理由であった。
Cimatron のハイブリッドモデリング機能で時間短縮を実現
モデリング時間は約半分になりました。この差は大きいですね。加工について、従来使用していたシステムは、きれいな加工面が得られることに定評があったのですが、Cimatronの加工面も大きな差はありませんでした。」(伊藤部長)
Cimatronのハイブリッドモデリング機能により、パラメトリックでのソリッドモデリングとぼかし面などの処理に強いサーフェス機能を組み合わせて使用し、フィレット付け、モデル結合削除など、大きな時間短縮が図られた。
「トリミングや角度付けなどが速くできるようになりました。形状同志の結合も、以前は、面と面の交線出して一つ一つトリムしていたが、ソリッドの塊岡志の結合ができるので楽ですね。」「従来のシステムでは随分時間がかかっていたモデリングした後の図面との比較も、ずいぶん短縮できました。」(製造部技術課課長 目黒雅裕氏)
パラメトリック機能やコマンド履歴により、形状の変更が簡単にできることで、設計変更にも迅速に対応できるようになった。
手直し不要の工程設計で、加工時間約25%削減
「CAMでは、勾配やRの測定が簡単に行え、抜き方向にグラデーションがつけられるなど、画面が見やすく、ずいぶん作業効率がアップしました。」(目黒課長)
パス清算も速くなり、コーナー加減速を使用することで加工時間が25%ほど短縮できた。また、自動CAMシステムも使用しているが、エアカットが多く、Cimatronでは効率的なバスが出せることで、25%程度の加工時間削減となっている。
シミュレーション機能で取り残し量やホルダの干渉チェックは毎回行うようにしている。
また、NCプレビュー機能では瞬時に残り代などの加工結果を見ることができるため、最適な加工方法を求めることで、手直しのない工程設計がされている。
加工テンプレートの活用
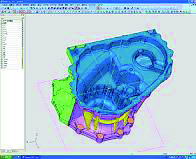
モデリング画面
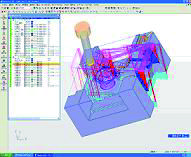
ツールパス表示
「CAMの性格としてマニアックなCAMと、初心者でも使えるCAMの二通りありますが、アルミダイキャストでは形状の起伏が激しくマニアックなCAMでなければきれいに削れません。Cimatronでは、CAMの設定項目が多く、非常に細かいところまでコントロールでき、自分の出したいバスを出せることがいいですね。」(目黒課長) これら細かい設定などのノウハウは、加工テンプレートに登録しておくことで、社内共有化され、入社したばかりの新人も含め、誰もが簡単に使えるようになっている。
同社では、まだ同時5軸機は持っていないが、テーブル回転タイプのマシニングセンタは使用している。Cimatronでは、ワークを傾けた加工でも干渉チェックが簡単であるため、オペレータが「傾けて削りましょうか」と積極的に言ってくるようになり、放電加工時間が随分減ってきたという。
穴あけ加工では、自動ドリル機能を活用している。加工方法であるシーケンスデータを登録するまで少し手間がかかったが、一度登録すると穴を自動認識して割り当てされるので、大きな効率アップにつながっている。
さらなる効率アップのために
「アルミダイカストには、穴あけから、2軸、2軸半、3軸まで必要です。今まで無駄なシステムを入れたこともあったが、Cimatronなら一台で可能です。」「Cimatronは、開発メーカーの将来性も考えて導入しました。長年使っていくものなので、いつまでも先端の機能を維持してもらいたいと思います。」(伊藤部長)
同社では、2006年Cimatronを2セット導入し、効果を確認したのち、2008年に3セット追加して合計5セットとなった。
「5台まで増え、その差は大きいですね。活用方法をもっと勉強することで、さらに効率アップにつなげていきたいと思います。」(伊藤部長)
このようにCimatronの能力を十分に生かし、更に有効な活テクノスでは、用法を追求し続けている。顧客ニーズに応え、常に効率化と品質向上に向けた精力的な取り組みを続ける同社は、Cimatronの進化とともにますます発展していくに違いない。
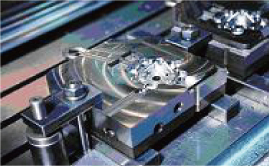
インタビューご協力
協力会社 | 株式会社寿原テクノス 様 |
---|---|
ホームページ | https://www.tts-eco.jp/ |
所在地 | 本社:愛知県稲沢市 |
創業 | 1964年 |
事業内容 | ダイカスト金型製造/ガラス、セラミック加工事業、超音波加工装置開発、製造、販売事業 |