ディプトロニクス株式会社は電子部品の不安定な流動、ウェルドライン、エアートラップの問題を一挙に解決
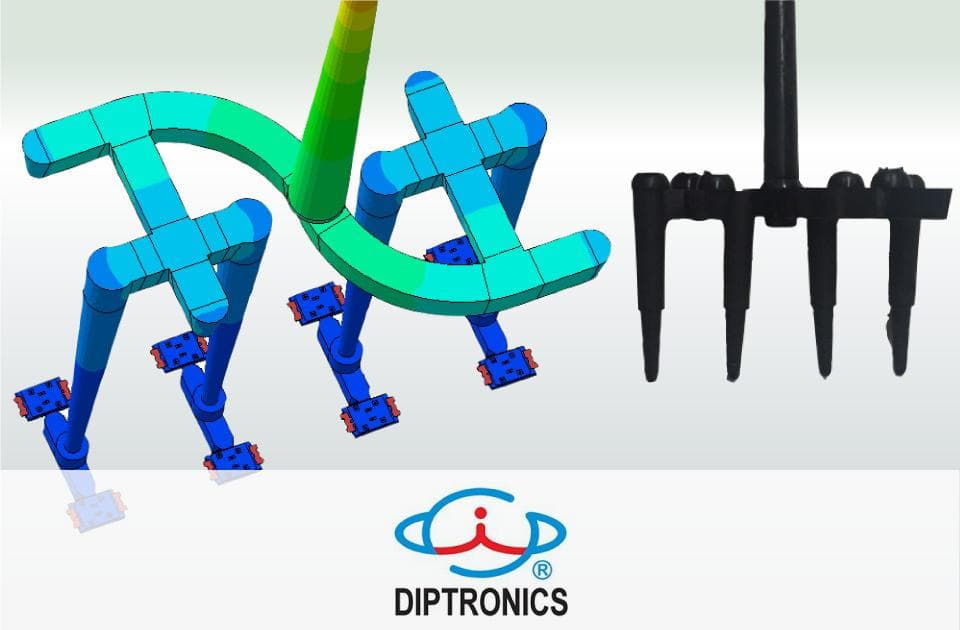
顧客情報
ディプトロニクス株式会社は1985年、台湾に設立され、スイッチ専業メーカーとして、ディップスイッチ、タクトスイッチ、ロータリースイッチ、マイクロスイッチ、スライドスイッチ、多機能スイッチ、LEDスイッチなどのさまざまなスイッチ製品の研究開発を行い、IATF 16949、ISO 14001認証を取得しています。その製品は、5大陸にわたる世界100か国以上で販売されています。
- 顧客名:ディプトロニクス株式会社
- 国名:台湾
- 産業:電子
- 導入ソリューション:Moldex3D Professional ;流動Flow、保圧Pack、冷却 Cool、そり変形Warp、Designer BLM
1.概要:電子スイッチのエアートラップ、ウェルドライン問題の改善
T3Cタクトスイッチは、ディプトロニクスの電子スイッチの中で最も生産量の多い製品の1つです。電子スイッチはスイッチへの接触することで、回路を導通させることを目的としているため、導通性はスイッチ製品における最も重要な性能です。しかし、このタイプの製品では、生産工程においてエアートラップ、ウェルドライン、材料不足などの問題が発生しやすく、導通不良を引き起こす原因となっています。 ディプトロニクスチームは、Moldex3D解析を使用して設計を変更し、充填バランスの取れた流動と成形サイクルの短縮を実現するとともに、エアートラップ、ウェルドライン、材料不足といった外観不良を改善するソリューションを導き出しました。流動解析を活用することで、製品の歩留まり率向上、コストの削減が可能となります。
2.製品の3つの課題
- エアートラップ、ウェルドライン、材料不足の不良を改善
- 不安定な流動のランナーを改善
- サイクルタイムの短縮
3.導入ソリューション:ランナー位置の設計を変更し外観不良を改善
ディプトロニクスチームは、Moldex3D解析を使用してランナー位置の設計を変更し、製品充填時におけるバランスの取れた流動、残留応力の低減、成形サイクルの短縮を実現しました。続いて、オーバーフローエリアの追加と製品の外観設計を変更し、エアートラップ、ウェルドライン、材料不足といった外観不良を改善しました。Moldex3Dを使用することで、最終的な全体の歩留まり率は39.68%向上し、生産サイクルも16%短縮できました。
4.ケーススタディ:解析と実験結果の一致
本事例でのT3Cタクトスイッチのサイズは3mm×2mm×0.6mmで、金型は8つのキャビティがある設計となります(図1)。内部キャビティの平均厚さは0.06~0.09mmで、一般的な製品に比べ、より難易度の高い加工技術が求められます。
図1 本事例製品の元の設計
Moldex3Dの解析で、流動が不安定であるという問題を確認できました。ランナー形状がフィッシュボーン形状のため、内側の樹脂の流動速度が外側よりも速くなるという現象が発生していました(図2)。
図2 サブランナー部でのアンバランスな流動
また、ランナー部の最大冷却時間が長すぎるために、成形サイクルも7~8秒と長くなっています(図3)。
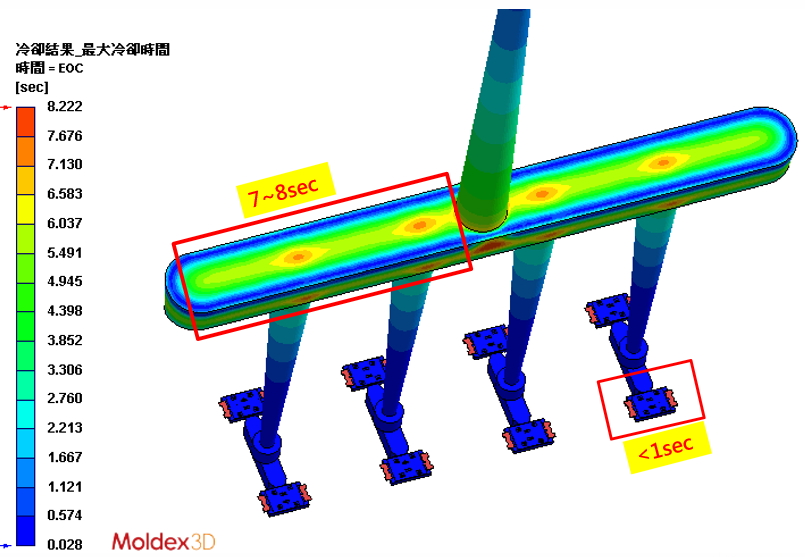
図3 冷却時間が長すぎることを示す解析結果
さらに詳しく観察してみると、ウェルドライン(図4の赤い線で示す部分)が製品背面の凹穴部分に集中していることで、流体が浸透しやすくなり、製品の導通不良を引き起こしていることが確認できました。
図4 潜在的なウェルドラインの位置
このほか、最大せん断応力(図5)が約6MPaと高すぎるために、プラスチックに亀裂や過剰な残留応力が発生しています。
図5 製品の高すぎるせん断応力
シミュレーション結果と実験から、流動の安定性に影響を与える主な原因はランナー設計であることが明らかになりました。そこで、Moldex3D解析と複数回にわたる実験検証の結果に基づき、不安定な流動の改善策として、元の設計に代わる新しいランナーを検討しました。ディプトロニクスチームでは最終的にS字型ランナーの採用を決定しました(図6)。
図6 S字型の新しいランナー設計
マルチキャビティのランナーバランスを調整することで、各キャビティを同時に充填・保圧できるようになります。キャビティの追加によって生産能力の向上につながるため、マルチキャビティの金型では、バランスの取れたランナーが非常に重要となります。ディプトロニクスチームは、Moldex3Dを使用して新しいランナー設計を評価したところ、不安定な流動(図7)、高せん断応力、長すぎる成形サイクルといった従来の問題がすべて解決されたことを確認しました。
図7 不安定な流動の問題が大幅に改善
S字型ランナーへの変更によって、せん断応力は7MPaから3MPaへと低下し(図8a)、最大冷却時間を8秒から5秒に短縮できました(図8b)。
図8 (a)せん断応力の低減に成功、(b)成形サイクルの短縮に成功
さらに、S字型ランナーシステムでは材料を11%節約でき、製造コストを削減できました(図9)。
図9 元の設計(左)と最適化された設計(右)のランナー重量比較
しかし、ウェルドラインやエアートラップ問題は、ランナーシステムを変更するだけでは解決できませんでした。背面にある深さ0.03~0.05mmの穴(図10a)やウェルドライン、エアートラップの問題を解決するために、外観を4つの外部エジェクターピン(図10b)に変更する必要がありました。
図10 背面の凹穴なし(a)、4つの外部エジェクターピン(b)に変更された最終的な最適化設計
実成形品の画像の通り、ウェルドラインの位置が成形品上部に移動しており(図11赤丸で示す部分)、元の設計から大幅に改善され、実モデルでの検証結果がシミュレーション結果とほぼ一致していることを確認できます。
図11 解析結果のメルトフロントと実験結果がほぼ一致
さらに詳しく観察してみると、凹穴のある元の設計ではウェルドラインがはっきりと確認できる(図12赤丸で示す部分)のに対し、凹穴をなくし、エジェクターピンの設計を変更した新しい設計では、製造上の品質要件を満たしていることが確認できます。
図12 元の設計(左)と最適化された設計(右)のウェルドライン比較
5.成果と結論
今回、Moldex3Dを使用することで、以下の結果を確認できました。
1.ウェルドラインの位置を効果的に制御
2.バランスの取れた流動
3.ランナー内の溶融樹脂を低減して材料を削減
4.成形サイクルの短縮
5.歩留まり率の向上
本事例は下記URLよりMoldex3Dの開発元であるコアテックシステム社の記事を参照しています。
https://jp.moldex3d.com/blog/customer_success/solving-the-unbalance-flow-weld-line-and-air-trap-issues-at-once/
ここまでお読みいただきありがとうございました。