ブダペスト工科経済大学はMoldex3Dにより金型冷却時間を18%短縮
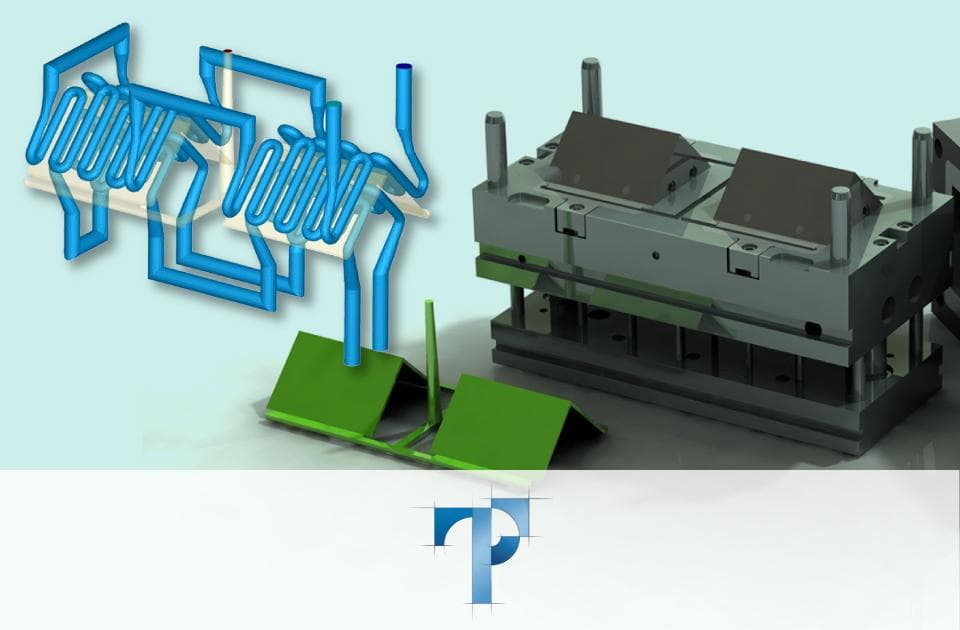
顧客情報
ブダペスト工科経済大学(BME)は、ハンガリー最大かつ最もよく知られている工科大学です。
機械工学部は学内最高峰の学部で、その高分子工学科は長い歴史を有しています。
- 顧客名:ブダペスト工科経済大学
- 国名:ハンガリー
- 産業:教育
- 導入ソリューション:Moldex3D Advanced ソリューション;流動解析モジュール Flow、保圧解析モジュール Pack、冷却解析モジュール Cool、そり変形解析モジュール Warp、Designer BLM
目次
1.概要:サイクルタイムの短縮とそり変形の低減に最も効果的な冷却回路設計
射出成形において、品質の劣る冷却システムでは温度分布が一定でないために冷却時間が長くなったり、そり変形が増加したりします。
また、鋭角形状を持つ製品では実装がさらに難しくなります。これまで冷却回路の最適化には多大なコストと時間が必要とされてきましたが、Moldex3Dの導入によってこれらの問題を大幅に改善することが可能となり、最適化プロセスの短縮やリソース消費の削減を実現することができます。
本事例において、BMEチームはスマートモールディングの利用によるワークフローの簡素化と冷却最適化による製造時間の短縮について紹介しています。
チームでは3種類の異なる材質の金型インサート(図1)について従来の方法によるものとMoldex3Dで作成した冷却回路(図2)を用いた実験を行い、さまざまな組み合わせ(図3)から、サイクルタイムの短縮とそり変形の低減に最も効果的な冷却回路設計を特定しました。
図1 異なる材質の金型インサート
図2 (a) 従来型冷却回路、(b) コンフォーマル冷却回路、(b1) 2キャビティ、(b2) 1キャビティ
図3 異なる材質の金型と冷却回路を組み合わせて実験を実施:
(a) P20金型と従来型冷却回路、(b) 銅製金型と従来型冷却回路、(c) DMLS:MS1金型とコンフォーマル冷却回路、(d) Hybrid:MS1と銅製のハイブリッド金型とコンフォーマル冷却回路
2.冷却に関する4つの課題
- 従来型冷却回路設計では3角屋根のような形状を持つ製品を適切に冷却することができない
- 適切に冷却されないと冷却時間が長くなり、生産コストが上昇する
- 不均一な冷却により深刻なそり変形が発生する
- 従来の方法での冷却最適化には大量のリソース消費を必要とする
図4 実験で使用したDMLS設計(上段)とHybrid設計(下段)の冷却時間
(a) 4秒、(b) 5秒、(c) 5.5秒、(d) 6秒後の取り出し時の温度分布
3.導入ソリューション:最適な冷却回路設計で、時間の短縮とそり減少を実現
今回は、3種類の材質の金型入れ子に従来型冷却回路とコンフォーマル冷却回路を組み合わせて実験を行いました。Moldex3Dの導入は、冷却速度の最適化、作業の簡素化、コストの削減に効果を発揮します。Moldex3Dのキャビティ内部可視化機能により、温度分布と冷却効率を検証することができました。コンフォーマル冷却回路を使用すると、冷却は均一になり、サイクルタイムが短縮され、そり変形が減少しています(図5、6)。
図5 シミュレーション開始後、取り出し温度に達したときの等値面:(a) t = 9.95 s、(b) t = 10.95 s、(c) t = 11.95 s、(d) t = 12.95 s
図6 金型開放時の表面温度:(a) t = 0 s、(b) t = 1.5 s、(c) t = 3 s、(d) t = 4.5 s
4.ケーススタディ:スマート冷却回路と、従来の冷却回路の比較事例
本事例の目的は、従来型冷却回路設計と「スマート」冷却回路設計の効率を比較することにあり、BMEチームは、成形サイクルを短縮し、そり変形を低減させるための実験を行いました。元の成形パラメータを用いたシミュレーションでは、製品のそり変形後の形状には変化が見られず、コンフォーマル冷却回路を使用した場合にそり変形の程度が従来型冷却回路よりわずかに低減していることを確認しました。また、P20インサート設計の場合にそり変形量が最も大きく、ハイブリッドインサート設計ではそり変形量が最小となりました(図7)。
図7 金型インサートのそり変形シミュレーション結果:(a) P20、(b) 銅製、(c) DMLS、(d) Hybrid
BMEチームはGOMの光学測定器で実際のそり変形を測定しました(図8参照)。銅製の冷却回路を使用した製品でそり変形量が最大となり、シミュレーションとは異なる結果となりましたが、これは実際の冷却時間が短かったためと考えられます(図9)。
銅製インサートの場合、外側は急速に冷却されますが、中心部分は高温のままなので、製品取り出し後に大きなそり変形が生じます。
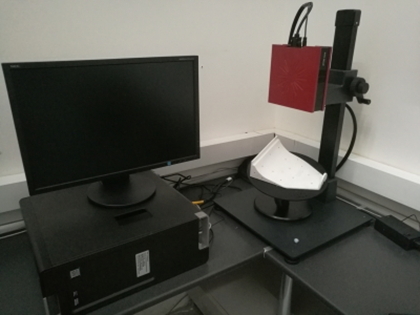
図8 GOMの光学測定器
図9 異なるインサートのそり変形の実際の測定:(a) P20、(b) 銅製、(c) DMLS、(d) Hybrid
続いて、実験による設計検証を行いました。従来型冷却回路とスマート冷却回路の検証結果は同じでした。実際のところ、銅製インサートを使用することで生産目標を迅速に達成することはできるものの、製品に深刻なそり変形が発生します。そのためBMEチームでは、最小のそり変形と最短のサイクルタイムを実現できるハイブリッド金型インサートが最適設計であると判断しました(図10)。Moldex3Dを使用することで、全体的な検証時間は4分の1に短縮され、リソース消費も削減することができました。
図10 実験とシミュレーション結果の比較
5.成果と結論
今回、Moldex3Dを使用することで、以下の結果を確認できました。
1.エネルギー使用量の削減
2.そり変形の30%低減
3.冷却時間の18%短縮
本事例は下記URLよりMoldex3Dの開発元であるコアテックシステム社の記事を参照しています。
https://jp.moldex3d.com/blog/customer_success/reducing-18-cooling-time-with-moldex3d/
ここまでお読みいただきありがとうございました。